Robust PTFE Material Designed Specifically for EV Battery Packs
As the demand for electric vehicles (EVs) continues to rise, ensuring their safety and reliability is paramount. At Porex, we provide cutting-edge EV battery vents to renowned companies worldwide. Our vents enable proper pressure equalization and quick gas release in case of failure, while effectively preventing dust and moisture infiltration into the battery.
With our expertise in material science, Porex offers customizable porous polymer solutions for various automotive venting needs. Our engineers can tailor a solution specific to your device, leveraging a range of materials, chemical compositions, geometries, assembly techniques, and additives. Experience the benefits of POREX Virtek™ PTFE EV battery vents for enhanced pressure equalization and ventilation.
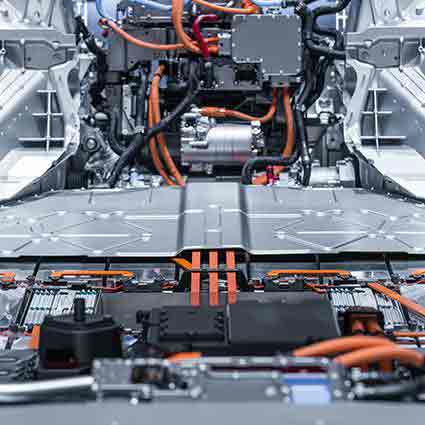
Electric Vehicle Battery Burst Vent
Protect your EV battery packs with high-performance Porex Virtek PTFE dual-stage safety vents without needing burst pins. Our fully-assembled vents give you a fast-release solution for thermal runaway and off-gassing that allows for both passive air venting and burst action in one component.
Options for customizing sintered PTFE EV battery vents
Related Resources
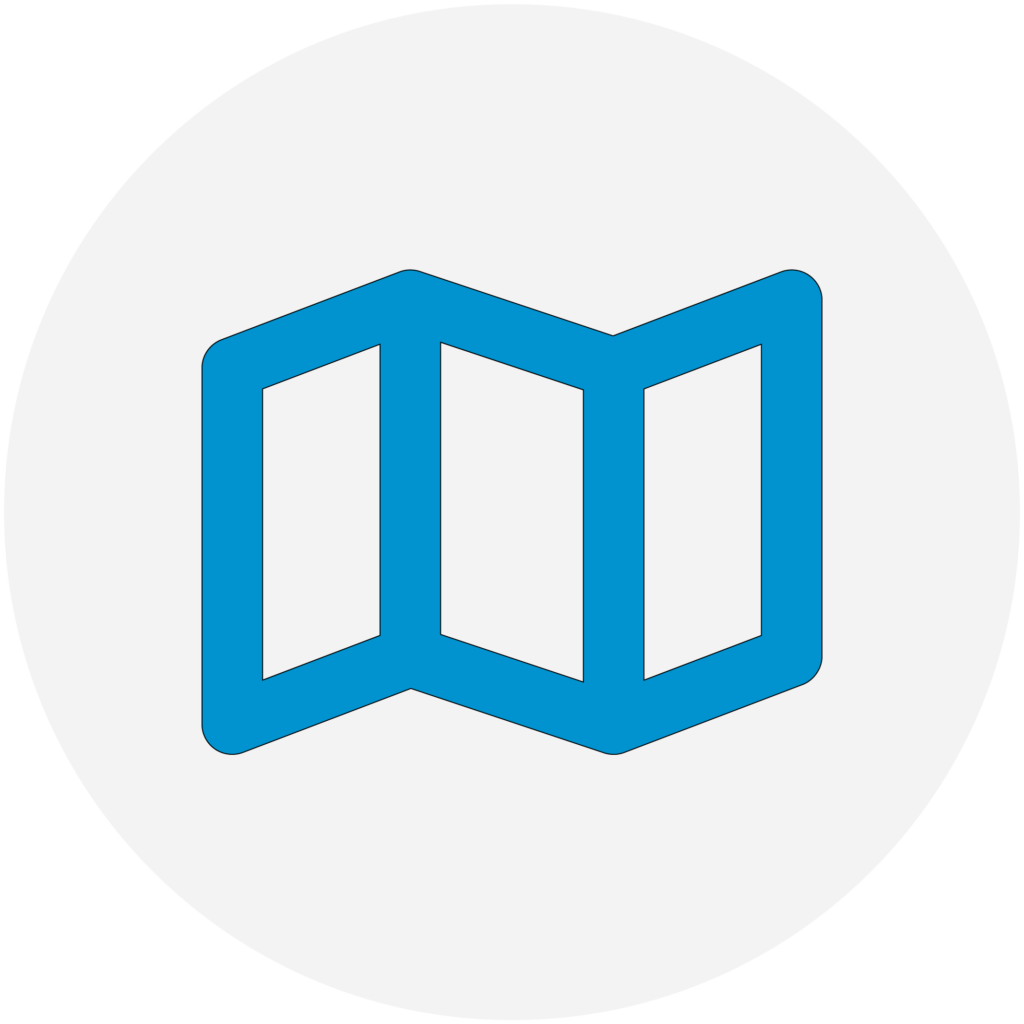
Porex Virtek® IP-Rated Protection Vents Brochure
Explore the portfolio of robust Porex Virtek® IP-Rated Protection Vents for electronics and automotive applications.
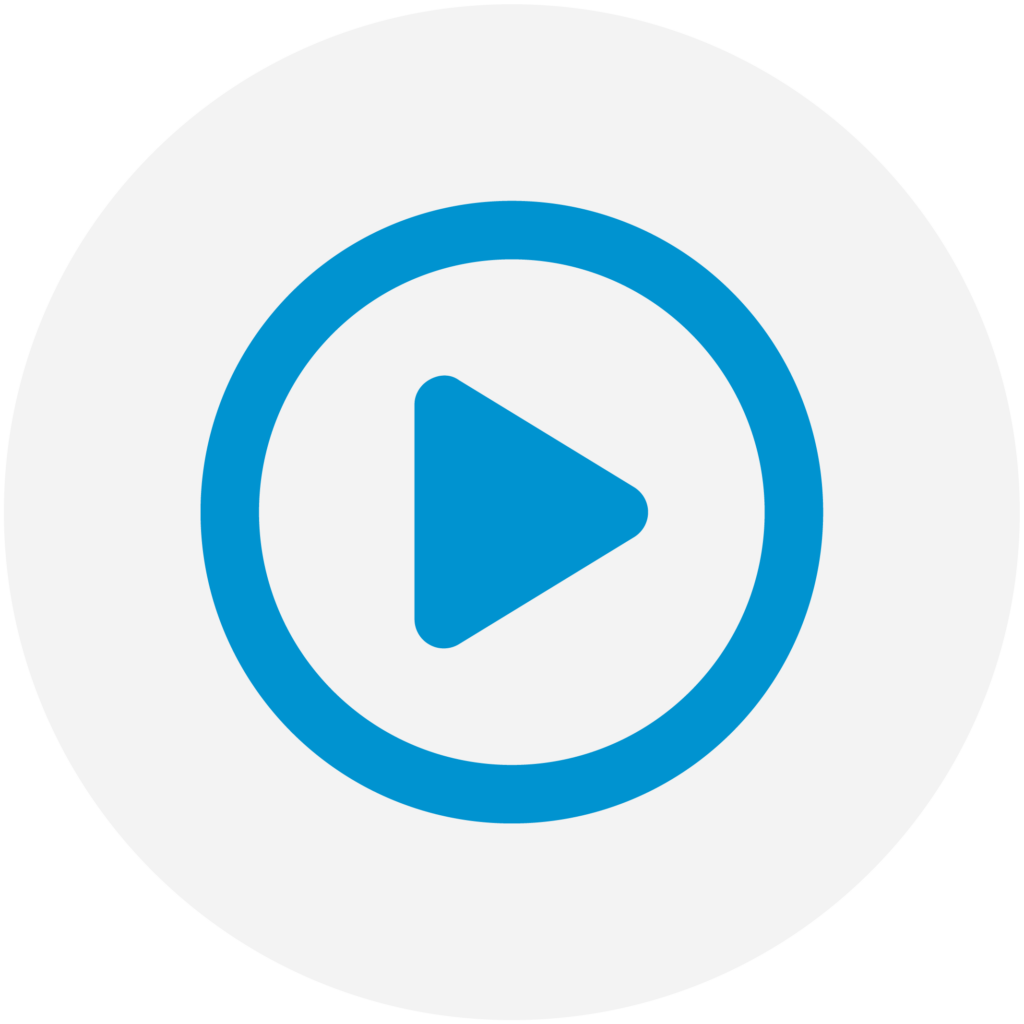
PTFE Video Venting Series: Porex Virtek PTFE vs ePTFE in a Battery Safety Vent Emergency Situation
A short video highlighting the advantages of Porex Virtek® PTFE over ePTFE in battery safety vent emergency situations.
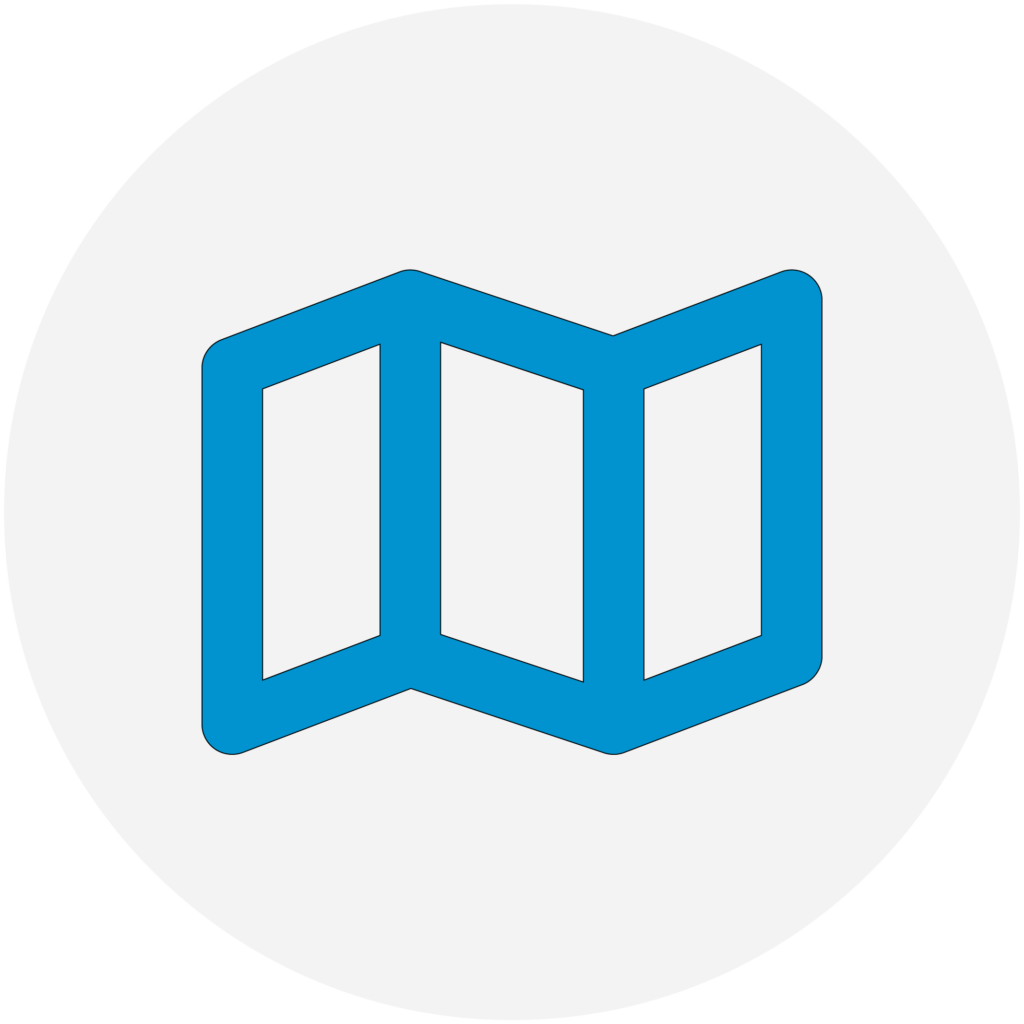
IP-Rated Vents for Automotive Applications Brochure
Discover the capabilities of POREX® IP-rated PTFE vents specifically designed for automotive applications, enabling rapid pressure equalization and ensuring effective protection.
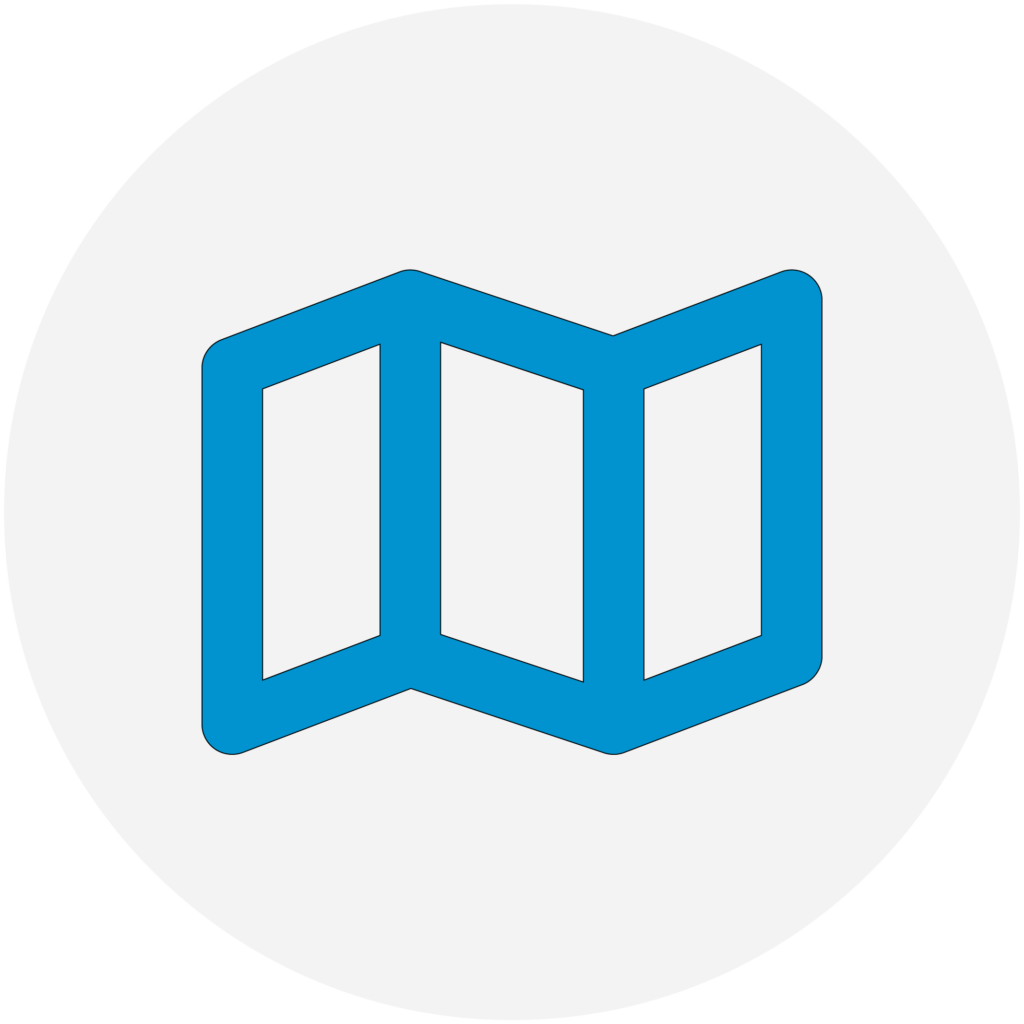
EV Venting Membranes Brochure
See why OEMs rely on Porex Virtek when it comes to automotive venting applications with PTFE hydrophobic and oleophobic membranes.